6 tips for assessing your toy manufacturer systematically
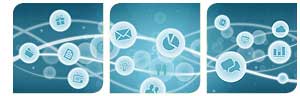
The importance of technical audit in choosing the right toy suppliers
Finding new suppliers can be tricky. After much effort spent in identifying a new toy supplier and negotiating the terms, have you ever wondered if they can fulfil your toys order and meet your expectations?
If your answer is yes, a toy technical audit done on-site is a great tool for understanding the prospective factory in term of capacity, quality, product safety, process, working conditions and other factors that are influential to smooth production. Although they are usually conducted by a third-party services provider, some buyers prefer to handle the audit by themselves to observe and interact with the factory first-hand.
Eurofins offers technical audits tailored for the toy industry. Contact us to find out more!
For those who want to conduct a technical audit on their own, here are some great tips from our technical experts so that you can assess your toy suppliers systematically:
- Quality management system of the factory
The safety of toys is always a critical concern to protect children and infants. The way that the factory assesses the risks of each toy is a tie break for every toy buyer. How much does the factory understand the regulatory requirement of your consumer markets? What certifications e.g. CE Marking and RoHS do they possess in term of toy safety? How does the factory integrate the quality strategy in its structure and organisation? Is the Quality Management System robust enough to ensure the compliance and conformity of your goods?
Practical tip: Before going for the factory tour, sit down and ask the management to explain to you in simple terms how they manage their QMS.
- Facility capability, capacity and Environment
The factory’s capability and capacity directly impact their production capacity and hence the lead time and delivery deadline. When checking the capability and capacity of the production facility, it is key to examine the production range, past/ current/upcoming orders, types and numbers of machines, machine calibration, and workforce size. You can also tell a lot from the factory’s existing clients.
The premises’ environment directly impacts the quality performances of the goods (layout, cleanliness, temperature, moisture rate, etc.). How does the factory maintain an appropriate environment to ensure product safety and compliance? For example, if you are producing electrical toys, the temperature of the storage area for lithium batteries must not exceed 60° C or 140° F or the batteries will go out of order easily.
Practical tip: Before the factory tour, ask the factory management to give you the daily/monthly production capacity, then during the factory tour try to understand the capacity of each line.
- Quality control system
Managing quality from the beginning point to the endpoint helps ensure your goods’ quality. Storage of raw materials and final products, control of incoming material, in-process and controls of the goods performed by an independent and qualified Quality Team are all the criteria to assess to ensure the factory has implemented the suitable system to assess and repair defects.
Practical tip: Ask for the QC manager to explain during the factory tour how he makes sure that all steps are quality safe.
- Production process
There are many aspects you can assess around the production process – are there mixing, moulding, painting and stamping processes inside the factory? If yes, are they in line with the proper and standard operation process? Is there on-site QC by the factory as promised? If yes, are they performing QC at 100% with clear guidelines? Is there any sub-contracting of work? If yes, how is the sub-contracting managed?
Practical tip: During factory tour, try to ask the management to detail the production, from the warehouse of raw materials to the finishing and packing section, following all steps.
- Testing capability and capacity
From choking hazards to restricted chemical substances, toy safety should be no stranger to any toy buyers and suppliers. Testing can be done in-house if the factory gets such capability, or at a testing firm. In most factories, a basic testing section is set up to handle fundamental tests such as choking hazards, cadmium content, total lead, and phthalates. When you are checking this part, you need to make sure if their testing standards fulfil your requirement. Alternatively, if the tests are done at a testing firm, you should check a few test reports to validate the practice.
Practical tip: During the factory tour, try to visit the internal laboratory of the factory if any, and ask for a demo of key testing methods.
- Skill and training of workforce
The skill and competency of workers is one of the key points to ensuring the factory can produce the expected quality within the expected deadline in a sustainable matter. A Quality Management System is useless without the right people to produce the goods. How does the factory manage its workforce, is the turnover high, how does the factory appoint, train and retain multi-skilled workers?
Practical tip: During the factory tour, after having asked for permission from the management, don’t hesitate to ask workers to explain what they are doing. The way they explain to you should show if they are were well trained or not.
The more relevant information you are able to gather and consolidate, the better risk assessment you can conclude from working with the new suppliers. The on-site technical audit in general takes one full day for a medium-sized factory so you would need to spare enough time with travel time included.
Apart from evaluating new suppliers, the toy technical audit is also an effective tool for improving existing suppliers’ performance by identifying shortcoming areas and implementing corrective actions. Establishing a solid buyer-supplier relationship helps boost work efficiency and lowers cost in the long run.
Whether you are planning to visit the toy factories on your own or hiring a third-party services provider, a technical audit will save you from various potential risks like delayed production, product fault and rejection and is critical to ensuring that you get off to the right start.