Four key performance and safety check of electrical goods before placing them to e-commerce markets
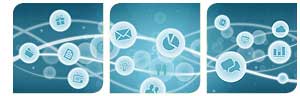
A search for ‘blender’, a common electrical kitchen tool, in a major e-commerce website in the USA lists more than 5,000 items from both renowned and lesser known brands. The total number of all home electronics available is much greater. Flooded by a huge number of listings, a key selection criterion that consumers opt for when choosing electrical and electronic products online is positive reviews. The inference is that positive reviews mean that the home electrical item being sold is safe and of good quality.
If you are importing electrical appliances for retail, no matter whether you are producing on OEM (Original Equipment Manufacturer) or ODM (Original Design Manufacturer) models, it is always crucial to implement robust quality control management at the factories to minimise risks associated with safety failures and quality defects.
On-site quality check by quality check (QCs) at factories or representatives from buyers is an essential part of quality control management. Here we highlight four major performance and safety checks that should be included in the quality inspection of most consumer electrical and electronic goods, whether they are electrical toys, kitchen tools or home lightings.
Battery Reverse Voltage Test
A battery reverse voltage test is conducted to determine whether a battery is able to withstand reverse polarity. Reverse polarity occurs when the battery is connected incorrectly, with the positive terminal connected to the negative terminal and vice versa. This test is critical to remove safety concerns because connecting a battery in reverse can cause damage to the battery, leading to an abnormal rise in temperature and possibly even to the battery exploding or catching fire.
During the reverse voltage test, the battery is connected to a power source in reverse and the surface temperature is recorded at the time of installation. The battery is usually left idle in the wrong position for four hours or more before it is removed and the surface temperature is measured again. Following the temperature check, the appliance is checked again for functionality to determine if it passes or fails the test.
Earth Continuity Test (Class I Appliance)
The Earth Continuity Test is a mandatory test for Class I appliances to protect users from electric shock. It is designed to measure the continuity of the earth connection within the appliance. For the European Union market, the reference standard is IEC 60335-1, while for the U.S. market, it is UL 1026.
During the Earth Continuity Test, a low current is passed through the earth conductor and the resistance is measured by a calibrated earth resistance tester. For both the EU and U.S. markets, the test fails if the more than 0.1 ohms is measured.
Electric Strength Test
The electric strength test, also known as dielectric strength test, is a crucial step in ensuring the safety and quality of electrical equipment. This test measures the ability of an electrical component to resist electrical breakdown when exposed to a high voltage. By subjecting the component to a voltage higher than its normal operating level, it is possible to determine if it can withstand electrical overloads and prevent electrical breakdowns.
Such a test, when carried out as part of an on-site inspection, is usually shorter than when conducted in the laboratory, following the test instructions specified in the test standards. During the test, high voltage is applied to the inspection sample by a calibrated hi-pot tester. The test is conducted on the different standards for different product types:
- IEC 60065 for audio products
- IEC 60335 / UL 60335 for household & similar electrical appliances
- IEC 60598 for luminaries
- IEC 60950 for IT products
Any sample that shows circuit/insulation breakdown, product damage or malfunction is considered to have failed the test.
Power Cord Strain Relief Test
The power cord strain relief test is a crucial part of ensuring the safety and durability of electrical appliances. This test evaluates the resistance of the power cord to strain and determines whether it can withstand normal wear and tear without compromising its performance.
During the test, the power cord is subjected to dynamic or static pulling forces to simulate real-world conditions, depending on which standard (IEC 60335, UL 60335 or UL 1026) is referenced. The objective is to observe any signs of cable damage or detachment from the plug. This helps to identify potential hazards that could lead to electrocution or other accidents.
Special Inspection Level 2 is usually recommended for this destructive test. For details, see further useful reading on ‘Explaining Acceptance Quality Limit (AQL) for product inspection’.
For sellers, ensuring that consumer electrical appliances are safe and of good quality is not only essential for customer satisfaction but also for their reputation. With our robust inspection knowledge and well-trained global inspection network, we can support your electrical and electronic quality inspection. Find more information here or contact us for a proposal.
Looking for details on electrical and electronic testing, or MET Mark? Find out more at Eurofins Electrical & Electronic.