What is the difference between quality assurance and quality control in garment manufacturing
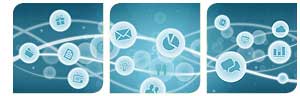
What is the difference between quality assurance and quality control in garment manufacturing?
What is the difference between quality assurance (QA) and quality control (QC) in the garment industry? Why is it important in textile and apparel production? These are two questions that we often receive from our clients when we discuss solutions for improving and maintaining the quality of their goods.
Quality Assurance vs Quality Control
Fundamentally, both QA and QC are programmes designed for quality management. The key difference lies in the approach – QA is a proactive approach that manages quality, while QC is a reactive approach that verifies quality. In other words, QA is a preventive measure to avoid quality issues, and QC is the identification of quality issues after they occur.
Another significant difference is where the programme takes place. As QA focuses on issue prevention, it involves the management of processes to make sure that things are right from the get-go. On the other hand, QC concerns raw materials, components and semi-finished/finished goods, as trained inspectors examine and assess the quality level of these tangible items. It is important to note that the two programmes are not meant to replace each other, but instead complement each other to maximise results.
Importance of QA and QC in garment industry
Quality assurance and quality control are widely adopted by different industries, as quality management is always a critical subject for manufacturing. When it comes to garment manufacturing, QA and QC are particularly crucial in this labour-intensive industry and defects from manual production can easily arise, causing quality issues and sometimes safety concerns. In a well-established QA and QC programme, the capacity of the factories, quality of materials, worker capabilities, and processes/workflows are reviewed and monitored closely before production begins, right through until the goods are loaded into containers. This undoubtably minimises the risks of having defective goods resulting from an incorrect production process, careless mistakes, faulty components, or other failure.
QA and QC, when implemented well, help to boost productivity and reduce unnecessary costs on re-work, shipment cancellation or recalls. They are especially beneficial for the following production scenarios:
- Large quantity orders with potentially higher associated risks
- Complex textile goods that require higher skill and technical levels
- Goods with greater safety concerns, such as childrenswear
Benefitting from QA and QC programme in economic downturn
The importance of comprehensive and effective QA and QC has become more prominent in recent years as garment buyers, suppliers and the general public have been hit by inflation. As well as the two questions noted earlier, there is a third query that is now on everyone’s mind – how can you still ensure quality when you are likely working with tighter budgets?
Times are difficult and consumers’ buying power is being directly impacted. They are unwilling to or unable to consume as they were doing before. Similarly, brands and retailers are facing hard times trying not to raise prices while maintaining profit margins, which means most buyers have to ask for cost reductions from their suppliers. Here, the dilemma is to what extent suppliers can accommodate buyers’ requests when prices of raw materials, labour and energy are on the rise. It could be suppliers that, in order to save costs, undercut production steps, reduce quality control processes, hire unqualified workers, or purchase lower quality raw materials and components. All of these shortcuts could seriously impact the quality of the final goods and ultimately be noticed by consumers.
However, by introducing a QA and QC programme, buyers can ensure that quality is not scarified for lower production costs. Stable quality will bring long-term benefits for brand reputation and consumer confidence, and mean that consumers will continue to buy from them during economic downturns. We have published a detailed step-by-step guide on how to set up a QA and QC programme for the garment industry so that buyers can build up their internal QA and QC programme systematically.
Suppliers can also run the same programme at their own production sites to demonstrate their commitment to quality production to existing and potential buyers. This is an effective showcase for client retention and new business cooperation.
In the implementation of the programme by first party (suppliers’ own teams) and second party (buyers’ own teams), it is crucial to monitor integrity in execution. In both scenarios, objective and unbiased observation might not be always the case, as supplier teams and buyer teams could face high pressure to meet production and shipping deadlines, which as a result might mean the QA and QC programme is not executed fully. Leveraging a third party for quality programmes is a very common approach in the industry.
More cost-effective implementation
For buyers or suppliers who are looking for a more cost-effective way to implement QA and QC programmes, the QA-QC Programme by Eurofins is an ideal choice. It is specially designed for the garment industry. Applicable to a wide variety of textiles and apparel, our QA-QC Programme can be customised for different scales of production, be it a single factory or multiple plants across various sites.
Alongside a chain of regular modules that integrates seamlessly into the production cycle to ensure quality at every step, our trouble-shooting module is where our expertise shines. In the garment production world, the width of an elastic band or the tightness of seamline sewing could be the make or break of good quality.
Together with representatives from factories, seasoned QA programme leaders and engineers can identify the root causes of quality issues and hence find solutions. The strong technical knowledge of our QA engineers in the textiles and garment industry, backed by over 15 years of experience in the field, allows us to figure out what has gone wrong with maximum efficiency, and most importantly find you the right solutions, documenting the problem in an actionable Corrective Action Plan (CPA) that factories can follow instantly. Each problem a factory faces can be a good learning experience on continuous improvement towards a right-first-time approach.
Be leveraging our existing programme, buyers and suppliers can get on-board easily without having to invest the time and effort into setting up a complex programme from scratch. Learn more about our QA-QC Programme for Garment and don't hesitate to book a discussion with us anytime.