The Whole Package: Get package testing solutions backed by sterilization and microbiology testing at Eurofins’ three San Jose sites
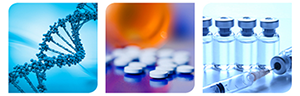
Wesley Harada, Operations Manager, Eurofins Infinity Package Testing, San Jose, CA; Luke Miller, President, Eurofins Infinity Laboratory Group, Inc.
Ensuring that a medical device or pharmaceutical product reaches its destination in its original condition is crucial. Package testing should be a part of the Biological Evaluation Plan (BEP), and as a best practice should be done early in the product development process to optimize both cost and time to market. This ensures that the packaging effectively protects the product during distribution; the packaging is compliant with any regulations; and the final packaging is on brand and works for the end user.
Eurofins offers full package testing expertise and guidance to test that product packaging is appropriate for the distribution of the product and ensure that the product arrives to the end user as desired. In our experience, we have seen situations where leaving the design and testing of the packaging to later in the design process has led to costly changes to both the packaging and the product, causing significant delays in launch, particularly when the design of the packaging does not withstand the rigors of transportation.
Another advantage of using Eurofins in San Jose, CA, for your package testing needs is a sterilization facility 15 minutes from the package testing facility, and a full microbiology lab in close proximity to both. We are seeing increased demand for both package testing and sterilization of devices with complex designs, often with embedded electronic components. As a best practice, we complete an R&D evaluation of the impact of testing on a small number of devices in partnership with our clients, before proceeding to validation and full production testing. Given the expense of implantables, there is a possibility, with client discussion, to use a placebo device with the same volume, dimensions, and weight in lieu of the full device in order to test the device packaging alone, when it is apparent that the rigor of the testing runs will damage the device inside the packaging.
We employ a variety of package testing methodologies in our ISO17025 accredited laboratory to simulate real-world transportation and handling conditions on small envelopes to large pallet sized configurations. These include:
Shock Testing – Evaluates how a package withstands accidental drops or impacts during transportation.
Vibration Testing – Assesses the impact of continuous movement and shaking that occurs in vehicle transit.
Environmental Conditioning – Exposes packaging to extreme temperatures and humidity to determine its resilience.
Sterile Barrier Integrity Testing – Ensures that no microorganisms or contaminants breach the packaging, maintaining the sterile barrier of medical and pharmaceutical products.
We collaborate with clients to design testing programs that align with industry regulations including ASTM, ISTA, and ISO standards. Whether ensuring pharmaceutical packaging stability under extreme temperatures or verifying the tamper resistance of consumer products, we partner with our clients to develop a testing protocol that fits the needs of the product and package under test.