Eliminating polo shirt defect as factory’s Production Engineer
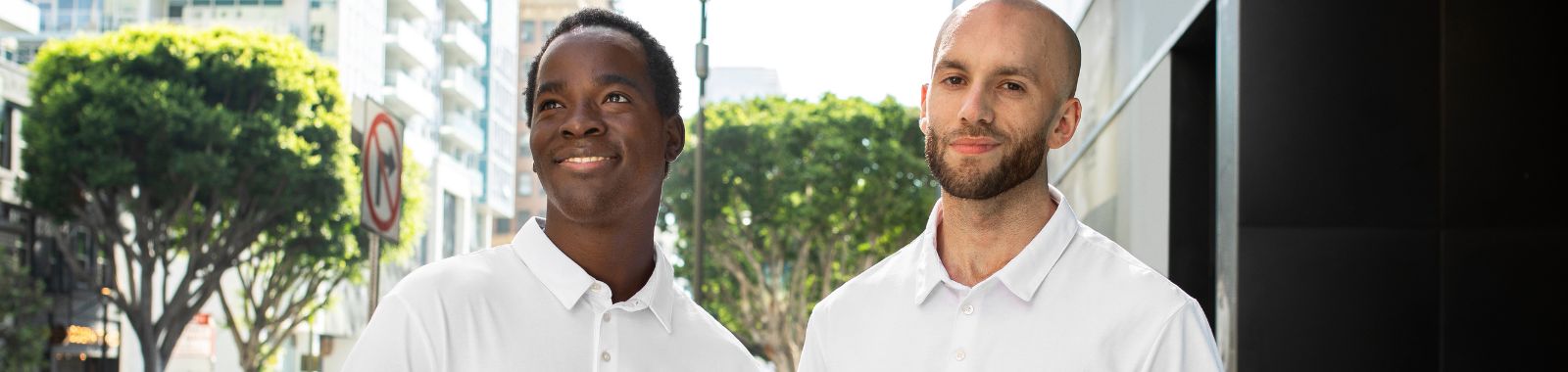

Achievement highlights
Eurofins’ QA-QC Team troubleshot this polo shirt production at early stage of manufacturing, reducing defective rate of collar at polo shirts from 20% to zero, and sparing 280,000 usd from the extreme rework cost of highly defective goods.
What was the issue?
Excessive end threads were found at polo shirt collars during quality check of production samples. The defect happened at about 20% of the production samples, representing 5% in quantity of 50 containers of goods in total.
Caption: Photos of protruding threads at collars
Why did the issue happen?
Upon request from customer, Eurofins QA-QC team examined the production planning, flow and process of the factory to find out underlying cause of the defect at collars. It could be easy for one to determine that the defect was caused by workmanship failure but a closer look has revealed that the absence of experienced Production Engineer in setting up and verifying each manufacturing process was the root-cause.
In garment manufacturing, as garment materials, designs and production methods vary, it is crucial to have a Production Engineer (or sometimes called Industrial Engineer) to design and validate the production steps, with reference to the products’ specification and production lines’ capabilities.
During this polo shirt manufacturing, loose end threads of 2 to 3 cm were left after knitting of the collars were completed. Mending operators were to manually hide the loose end in the collar edge tubes before assembly process took place. Trimming the entire loose thread would not work as this would set the knitting loose and the whole component would fall apart.
Issue happened when mending operator, in this case, hided all three loose threads (three colour tipping) at collar corners with only one-shot hiding. Also, end trimming of the protruding thread was not done properly everytime as no SOP was available.
How did we fix it?
Having performed the diagnosis on-site, our QA-QC team identified the cause of collar defect promptly as illustrated above.
Our team picked up the role of Production Engineer of the factory, and re-constructed the production steps of this polo shirt to eliminate the defect:
- Mending operators’ hiding process was corrected from one-shot to two-shot (see a video showing the corrected process). With two-shot hiding, loose end threads would be hidden in the collar edge tubes perfectly. It is quite a normal practice in the industry that multiple shot of hiding is required when there are more than two end loose threads on one single side, as experience has told our team.
- SOP was created to capture the hiding process and endtrimming process so all operators can follow easily.
- Mock-up pieces were made and demonstrated to operators in a dedicated training session.
Caption: On-site diagnosis taking place.
Caption: Operators at dedicated training session on two-shot hiding process.
Caption: QC examining collars and whole polo shirts regularly.
On top of these corrective actions, defective pieces were reviewed and reworked where possible as remedy. Rejected pieces were isolated completely.
To ensure true improvement, regular monitoring was of course carried out by our team with Daily visit to the factory and production inline, and QC running checking quality check. Corrective Action Plan was documented so factory can take note and improve for future similar orders.
What were the results?
It was very motivating that no identical defect was found after all the corrective actions were implemented. The defective rate of this defect was brought down from 20% to zero in the mass production of one million pieces.
If the goods had arrived the brand’s warehouse, it would have costed at least 280,000 usd to return and rework at origin country and ship the reworked goods back to selling market again. Apart from such direct expense, the possible delay in stock availability for retail and complaints from consumers would have led to extra loss in brand reputation and finance.
Eurofins’ QA-QC Programme ironed out these issues were ironed out promptly, offering maximised cost effectiveness that any fashion brands and retailers can count on.
Caption: Polo collar of perfect condition after corrective actions.
Caption: Polo shirt with collar in good condition, ready for sales.
This case highlights the importance of a Production Engineer in smooth and efficient garment production, and this is not a part that any garment factory should overlook.
Our QA-QC Team can support a single garment production project or be your outsourced Production Engineer at designated factories to monitor outputs quality. Check out how our QA-QC Programme for Apparel and Garment Industry can help!




© Eurofins Assurance 2024 Personal data protection policy